Why HoptiAM™?
HoptiAM™ is the brewing industry maintenance management solution designed to optimize the performance of high-value equipment.
HoptiAM™ is designed to be easy to use and quickly implemented. For a craft brewer to be successful, brewing, canning/packaging, and delivery equipment needs to be maintained properly. This ensures minimal downtime and maximum production. HoptiAM™ provides you with a proactive maintenance program that will minimize equipment downtime, loss of production, and missed shipments.
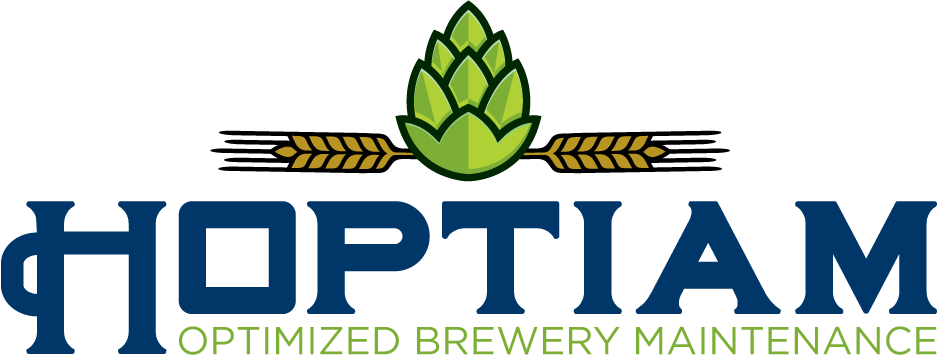
HoptiAM™ helps you plan, optimize, execute, and track maintenance and other management activities along with the priorities, people, materials, tools, and technical information associated with managing and maintaining your physical assets. HoptiAM™ was developed to provide an easy to use solution that can be quickly implemented in breweries of all sizes. An intuitive user interface with preloaded equipment and maintenance tasks and schedules specific to the brewing industry such as mashing tun maintenance, cleaning, grain mill maintenance, tank/vessel preservation, and boiler maintenance enables your staff to use HoptiAM™ with minimal training and upfront setup work.
HoptiAM™ also allows the user to create customized tasks and maintenance schedules to suit their specific needs. HoptiAM™ ensures your equipment will be kept in better condition through appropriate preventive maintenance and reduces the time required to perform that maintenance by providing intuitive maintenance instructions. You’ve invested a lot in your equipment, HoptiAM™ helps you protect that investment and spend more time making beer and less time thinking about maintenance.
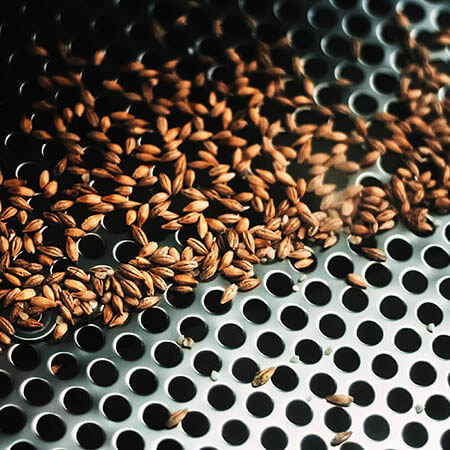
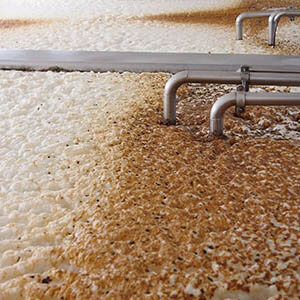
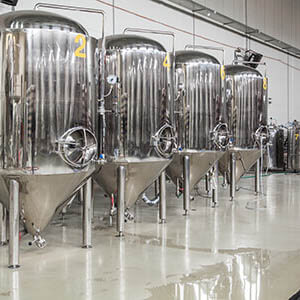
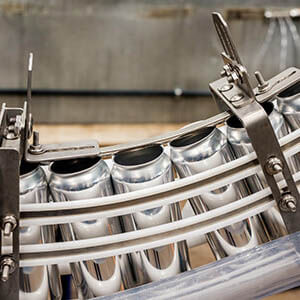
Gain real-time status and insight into equipment performance.
Data is translated into actionable knowledge, enabling continuous improvement.
Asset Management
Downtime due to equipment failure is the last thing a craft brewery needs. Outside of time and money for cleanup and repairs, it is critical to avoid lost production time – which leads to unfulfilled orders, frustrated customers and lost revenue.
Your brewery depends on using the right products and performing planned maintenance (PM) at the correct intervals. The easiest way to maximize your output is to properly maintain your equipment so your operation runs efficiently. HoptiAM™ allows you to achieve this by automatically scheduling PM for your assets – listing the correct chemicals, parts, tools, and procedures for proper maintenance.
HoptiAM™ was created with the end user’s needs in mind, Designed from the ground up to be a flexible software package, ASI will work with you to tailor HoptiAM™ to your specific needs.
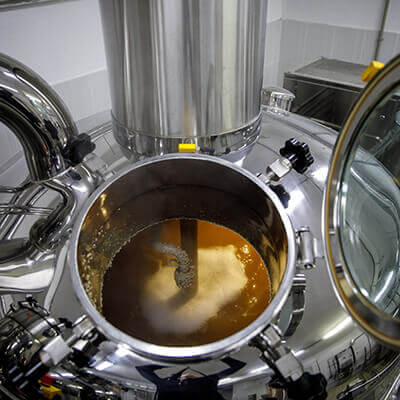
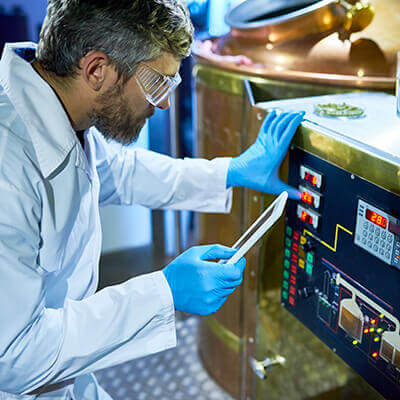
Safety within Brewery Maintenance
Breweries, like any production facility presents safety concerns for workers. Packaging machines, heated vessels, moving machinery, and forklifts each present unique safety hazards. Maintenance personnel and operators need to be aware of and how to mitigate hazards involved with maintenance activities.
Providing the maintenance technician with the proper Lock Out/Tag Out procedures prior to performing maintenance is critical. Identifying signage and location to be placed on the equipment while maintenance is being performed is also critical for operators to prevent injury to themselves or others. HoptiAM™ provides maintainers with the proper safety information they need for each piece of equipment.
HoptiAM™ is Built on Analytics
Here are just some of the unique features HoptiAM™ users enjoy:
Reduced implementation
and training costs… PLUS highly competitive licensing costs
Seamless System Integration
Supports Compliance
Simple and Intuitive
Ability to Customize
Latest Web-based Technology
Incorporates the Latest Technology
Case Study
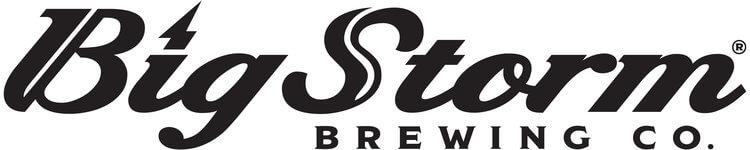
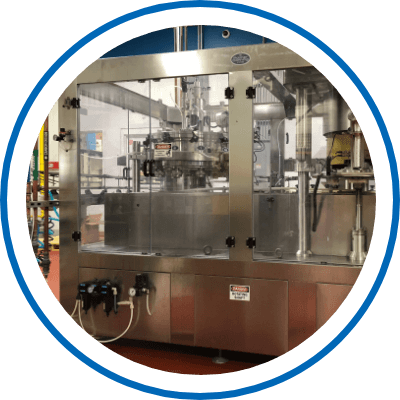
Canning machine at Big Storm Brewing
Manufacturer’s specifications for maintenance were followed.
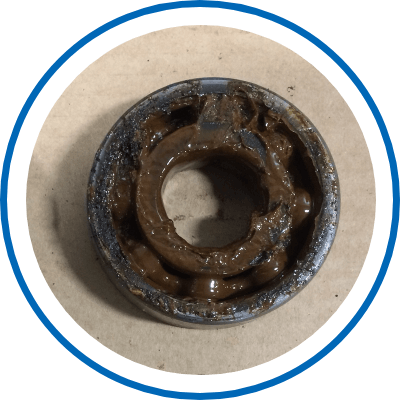
Monitoring
Early in life cycle noticed rust seeping out of bearing housings and flanges. Machine began to run rough as time went on.
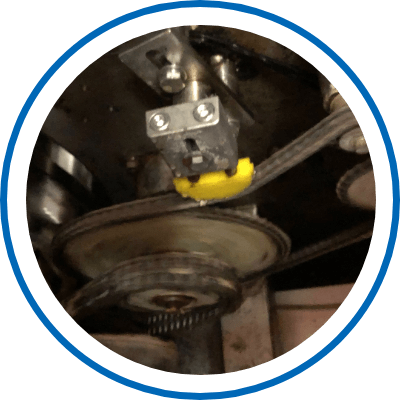
Root Cause Analysis (RCA)
Investigation led to removal and inspection of the bearings. Machine had standard shielded bearings (vs. double-sealed) installed in wash down locations.
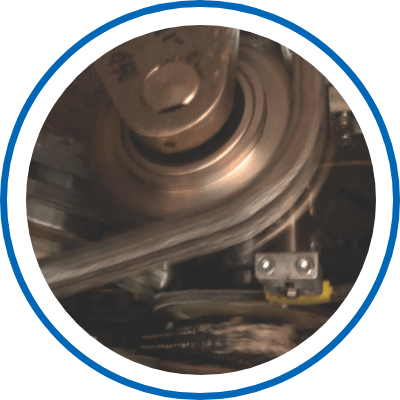
Corrective Action
Prior to bearings failing they were strategically scheduled for replacement in between canning runs to keep the machine in operation and not miss orders.
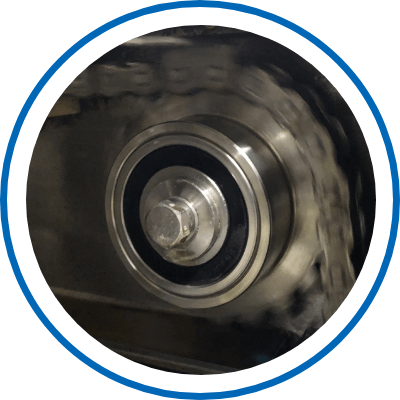
Result
If the bearings had failed severe damage may have occurred to bearing seats resulting in extensive downtime and repairs. The bearings were upgraded with stainless steel double-sealed bearings, extensive repairs/downtime avoided.
Get Insight into Equipment Performance with Real-Time Status Updates
HoptiAM™ is a module-based system which can be tailored to your needs. HoptiAM™ modules include:
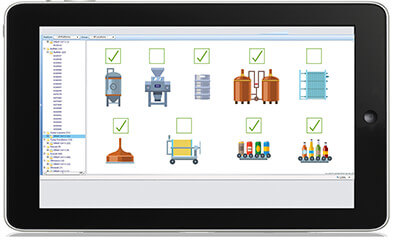
Asset Manager
The Asset Manager module identifies, defines and documents assets. With the Asset Manager, you can add assets and define attributes such as serial number, location, warranty, and vendor information. The Asset Manager allows you to group assets into physical and functional hierarchies and identify assets via QR code or RFID tags. The interface provides intelligent searches for quick access to a variety of lists and information about your assets. For spares, parts, and consumables, Asset Manager will track quantities on hand, establish reorder points, and identify vendor information.
Live Library
With the Live Library, all available maintenance and operating procedures and resource information are at the fingertips of any user in any location. Live Library stores, associates and classifies technical data associated with individual assets and provides an intuitive, searchable interface for easy access. Live Library also allows the user to print documents and add notes and comments to documents to promote knowledge sharing.
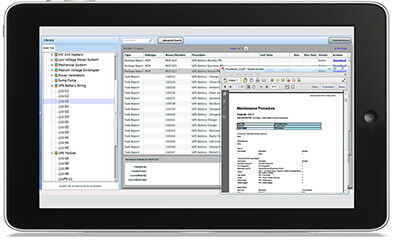
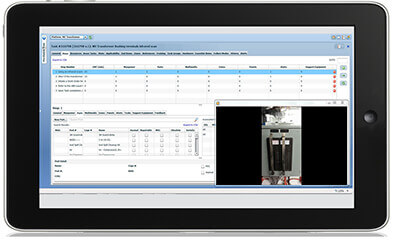
Task Developer
Develop the procedures and identify all of the resources needed to support your assets. Task Developer identifies resources needed to perform preventative and corrective maintenance tasks and groups these tasks into maintenance packages. The Task Developer can also generate electronic maintenance manuals, standard operating procedures (SOP) and emergency operating procedures (EOP). Revisions can be tracked and releases controlled. Task Developer also creates automated checklists for use with the OptiAM® mobile and FleetChek™ mobile applications.
Maintenance Optimizer
Optimize your maintenance schedule based on individual asset usage and environment to minimize downtime or cost. The Maintenance Optimizer provides a full featured work order management system to schedule, manage, execute and document maintenance workload. It also can schedule actions such as contract or warranty renewals, planned upgrades and set alert triggers to generate automated work orders based on inputs from inspections, PdM or equipment monitoring systems. The Maintenance Optimizer provides near real-time equipment status to other modules in OptiAM®
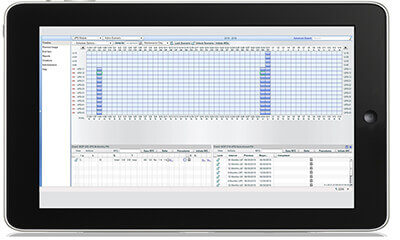
Software as a Service
Developed using the latest rich Internet application technology and standard data formats, the HoptiAM™ environment delivers an intuitive and consistent user experience across all major operating systems.
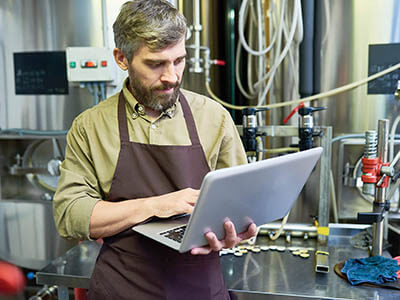
SaaS
HoptiAM™ is offered as Software as a Service (SaaS) on a monthly subscription basis. Affordable monthly or annual plans let you implement HoptiAM™ with no risk and minimal upfront costs. All you need is a web browser and an internet connection.
Some of the many advantages of the SaaS solution include easier setup, lower initial cost, painless upgrades and no system administration. The hosted solution provides for data security, redundancy and backup. Our servers are hosted by Amazon Web Services, in a professionally managed hosting facility which provides for redundant backup power, fire suppression, redundant tier 1 Internet access and biometric controlled physical access, ensuring your data is safe and secure.
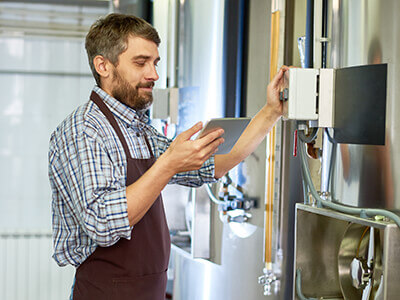
HoptiAM™ Mobile Application
Improve maintenance accuracy and efficiency by accessing technical data and documenting work at the point of performance. These applications allow you to operate offline or online via cellular or Wi-Fi connection. The applications manage and synchronize work orders in real time and gives you access to searchable technical data and attached multimedia such as instructional videos. You can scan parts for work orders and inventory control using optical codes or RFID. HoptiAM™ Mobile uses text and media capture to record results and capture electronic checklist results.
Book a Demo
Learn how HoptiAM™ will benefit your business. We provide a customized tour and answer your questions.
HoptiAM™ Guide
Download our HoptiAM™ brochure for an in-depth guide to our Optimized Maintenance Management solution.
What our HoptiAM™ clients are saying…
Corporate Headquarters
440 Viking Drive, Suite 230
Virginia Beach, VA 23452
Corporate Office
6255 Lake Gray Blvd., Suite 4
Jacksonville, FL 32244
USA Offices
Crystal City, VA
Havelock, NC
Oklahoma City, OK
Patuxent River, MD
San Diego, CA
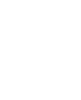
Get in Touch
904-637-2020
Follow Us
Email Us
"*" indicates required fields