About RCM Training
Our Reliability Centered Maintenance (RCM) training program provides you with the fundamental concepts necessary for determining appropriate preventive maintenance requirements and other failure mitigation strategies. RCM applies to any industry that requires safe, reliable, and cost-effective performance from their physical assets including, but are not limited to Defense, Aerospace, Maritime, Transportation, Manufacturing, Pharmaceutical, Food Processing, Chemical Processing, Petroleum, Mining, Facilities, Agriculture, Alternative Energy, Energy Distribution, and Power Generation.
The Goal
When completing our training program, you will have the knowledge necessary to apply RCM analysis to develop effective, RCM-based maintenance programs. RCM training provides to attendees the principles and analysis techniques needed to realize required capability and reliability of physical assets at the minimum possible cost and lowest risk through the mitigation of equipment failures. Learn the analysis techniques used around the world by military and public and commercial sector organizations to define and deploy world-class maintenance programs. We provide you with the knowledge and experience necessary to begin applying a logical and comprehensive SAE JA1011 compliant RCM process at your facility or on your fleet.
SAE JA 1011
(Society of Automotive Engineers)
The technical standard: Evaluation Criteria for RCM Processes. This standard outlines the minimum criteria required for any process to be called RCM by applying 7 standard questions:
- What is the asset supposed to do and what are its associated performance standards?
- In what ways can it fail to provide the required functions?
- What are the specific causes of each failure?
- What are the consequence when each failure occurs?
- In what way does each failure matter?
- What task or action can be performed proactively to prevent, or to diminish to a
- satisfactory degree, the consequences of the failure?
- What must be done if a suitable preventive task cannot be found?
The outcome of this process is a systematic maintenance program that prioritizes up-time and efficiency at the lowest possible cost. It also provides a baseline for measurement and future process improvement.
Some of the major topics we cover:
- Equipment partitioning
- Failure modes, effects, and criticality analysis
- Preventive and Predictive maintenance strategies
- Equipment failure behaviors
- Identifying operating risk and consequences
- Run-to-failure strategies
- Equipment criticality analysis
- Potential failure identification
- Condition based maintenance
Types of RCM Training
RCM affects operations at all levels of the organization. The RCM course offerings reflect the different needs of executives, reliability managers, and others who interact with the RCM decision-making process and/or daily maintenance schedule.
For Executives & Managers
RCM 100 • 1 hour • RCM Executive Overview
For Reliability Managers
RCM 101 • 2 days • Fundamentals of RCM Analysis
RCM 201 • 2 days • Advanced Topics
For RCM Support Staff
RCM 102 • 4 hours • Terminology and Concepts
Benefits of RCM Training
Reliability Centered Maintenance (RCM) method achieves optimal levels of economy, availability, and safety by developing and applying cutting-edge systems engineering and supportability analysis tools, processes, and expertise.
RCM strategy provides critical insights into equipment performance, identifies system improvements, optimizes operations & support, enhances business decisions, and achieves measurable life-cycle cost savings.
- Increased confidence in capital equipment decision making
- More reliable plant and operating equipment; improved machine uptime
- Optimal solutions for responding to failure modes
- Ability to audit performance equipment
- More accurate planning and budgeting for capital equipment
- Deliver to management the highest possible plant utility and performance
- Make sense of and leverage failure data
- Make informed risk decisions on paper using quantifiable (and explainable) formula
Who is RCM for?
RCM training is beneficial to the military, municipal & commercial sectors, specifically:
- Fleet/asset managers
- Maintenance planners/managers
- Reliability managers/engineers
- Field service representatives
- Logisticians
- Maintenance technicians
- Supportability professionals
- Executive management
Pricing
Training $799 USD per student.
For more information please contact us at: edu.pierian@androsysinc.com
Group Discounts Available.
Choose Your RCM Training
RCM 100
RCM Executive Overview
A high-level overview of the Reliability-Centered Maintenance (RCM) process, to include benefits, data requirements, and the role of RCM in an overall asset management program.
- A management-level understanding of RCM and its component processes
- An understanding of resources involved in undertaking an RCM effort (Who, What, When, and How)
- What benefits and return on investment are traditionally expected from an RCM effort
- RCM total outcomes
The Overview will provide what it takes to implement the RCM process and what benefits you can expect upon implementation. In addition, it provides examples of the common pitfalls an organization should avoid.
RCM 101
Fundamentals of RCM Analysis
An introduction to the RCM process that provides the instruction and practical application required to apply Reliability Centered Maintenance Analysis to physical assets. The course provides instruction in a Society of Automotive Engineers (SAE) Standard JA1011 compliant RCM process. This course provides training designed to provide an understanding of RCM disciplines as they relate to developing efficient preventative maintenance programs. Intended for personnel who will perform or facilitate RCM analyses.
- Theory and practical experience needed to implement and perform RCM analysis
- Experience developing effective failure management strategies
- An understanding of RCM’s role within asset management
- Ability to identify opportunities that may warrant a more in-depth reliability analysis
- An understanding of PSA disciplines as they relate to developing efficient
preventative maintenance programs
You’ll walk away with the instruction and practice needed to apply Reliability Centered Maintenance (RCM) Analysis to physical assets. The course provides instruction in a Society of Automotive Engineers (SAE) Standard JA1011 compliant RCM process.
This introductory course provides training designed to provide an in-depth understanding of RCM disciplines as they relate to developing efficient preventative maintenance programs.
RCM 102
Terminology & Concepts
An introduction to the RCM process and related concepts and terminology. Participants will gain general knowledge of RCM principles, what information is required to perform RCM, and how that information is used. Intended to provide basic knowledge to staff who will participate in RCM analysis and managers who may want a more detailed overview of the RCM process.
- General knowledge of RCM principles
- What information is needed to perform RCM and how that information is used
- A working understanding of the planning and preparation phase of RCM Analysis
- Knowledge of the various support roles and their responsibilities within an RCM Analysis
You’ll walk away with the knowledge needed to participate as a supporting role for a RCM effort. The course provides a high-level overview in a Society of Automotive Engineers (SAE) Standard JA 1011 compliant RCM process, including the 4 major elements of the RCM process.
This course provides the understanding for a support role interface during an RCM Analysis. Support roles include Equipment/System Subject Matter Expert (SME), System Engineers, Data Analysis, Logistics Support, Maintenance Planners and Maintenance Managers.
RCM 201
RCM Advanced Topics
An in-depth review of advanced topics that an analyst or facilitator may encounter while accomplishing an analysis effort. This course includes case studies that address project execution and implementation issues. Intended for experienced RCM analysts who are responsible for implementing the process.
- A deeper understanding of the theory, processes, and procedures needed to supervise, implement, and perform RCM analysis.
- Topics and knowledge for the more advanced RCM analyst with experience
- Examination of RCM Case studies to address implementation and integration issues.
- An understanding of RCM’s role within asset management
If you’re an RCM Analyst who has experience participating in RCM Analysis efforts but you need a better understanding of what is needed to lead an RCM effort, the Advanced RCM Topics Class is the course to attend. You will walk away with the knowledge as an understanding of the responsibilities to lead and implement an RCM program.
The course provides detailed instruction in a Society of Automotive Engineers (SAE) Standard JA1011 compliant RCM process as well as common pitfalls encountered during an implementation effort.
Training Information Request
We’re happy to answer you questions about our training courses. Get in contact with our team today.
"*" indicates required fields
Call or email for pricing, registration information, discounts for multiple attendees and government employees.
Corporate Headquarters
440 Viking Drive, Suite 230
Virginia Beach, VA 23452
Corporate Office
6255 Lake Gray Blvd., Suite 4
Jacksonville, FL 32244
USA Offices
Crystal City, VA
Havelock, NC
Oklahoma City, OK
Patuxent River, MD
San Diego, CA
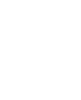
Get in Touch
904-637-2020
Follow Us
Email Us
"*" indicates required fields