OptiAM®
The EAM & CMMS software package that works the way you do.
OptiAM® is an Enterprise Asset Management Software (EAM) System
Developed by Andromeda Systems Incorporated and designed to optimize maintenance programs and support for assets ranging from simple to very complex.
It applies proven supportability and maintenance analysis techniques to ensure maximum asset availability and operational readiness. The system features automated maintenance optimization scheduling and real-time visibility of ongoing maintenance activities, making it easy to manage assets efficiently. With its flexible role-based security model, OptiAM® can support any organizational structure, and a mobile application enables point-of-performance recording of maintenance activities. This enterprise-wide solution is an ideal choice for organizations looking to optimize their asset management processes.
Originally developed to meet the demanding standards of the U.S. Military with inputs from experienced maintenance personnel, OptiAM® is user-friendly and can be easily and quickly implemented to meet asset management and tracking needs of any industry.
OptiAM® is Built on Analytics
Here are just some of the unique features OptiAM® users enjoy:
Reduced implementation and training costs
Highly competitive licensing costs
Designed to support seamless integration with existing applications and databases
Standards-Based Architecture
Supports compliance with industry standards such as ISO-55000, SAE GEIA-STD-0007, SAE JA1011, and the S Series ILS Specifications
Ability to customize interfaces and processes shortens learning curves
Incorporates latest technology including mobile, Radio Frequency Identification (RFID) and Predictive Maintenances
Simple and intuitive interface
Latest Web-based Technology ensures maximum reliability and security for every operation
Get Insight into Asset Performance
with Real-Time Status Updates
OptiAM® is a module based system which can be tailored
to your needs. OptiAM® modules include:
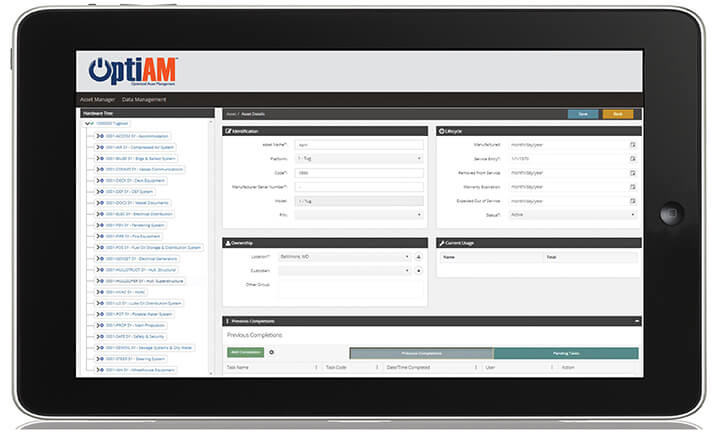
Asset Manager
This module identifies, defines, and documents assets. You can add assets and define attributes such as serial number, location, warranty, and vendor information. The Asset Manager allows you to group assets into physical and functional hierarchies and identify assets via QR codes or RFID tags. The interface provides intelligent searches for quick access to a variety of lists and information about your assets. For spare parts and consumables, Asset Manager will track quantities on hand, establish reorder points, and identify vendor information.
Hardware Builder
Hardware Builder is used to define the physical structure of the assets being managed by OptiAM® which is then used in many other modules. The user can breakdown the hardware in a much or as little detail as required. For each node in the hardware breakdown, users can define acceptable manufacture and part numbers for application on assets. The system supports building of both physical and function hardware trees for detailed analysis using other OptiAM® modules.
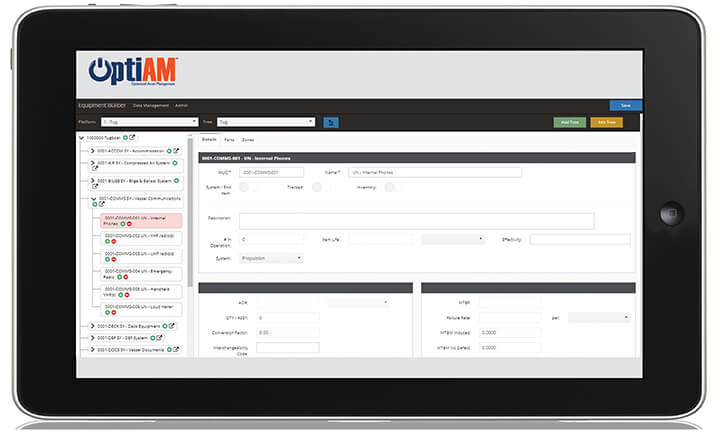
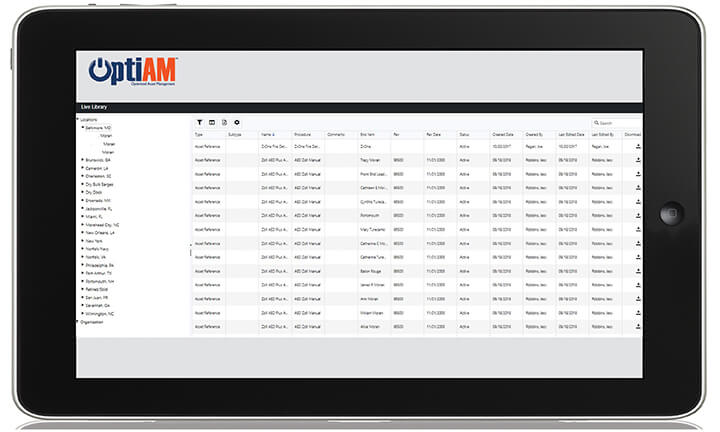
Live Library
With the Live Library all available maintenance, operating procedures, and resource information is at the fingertips of any user in any location. Live Library stores, associates, and classifies technical data associated with individual assets providing an intuitive, searchable interface for easy access. Live Library also allows the user to add notes and comments to documents as well as utilizing a print function to promote knowledge sharing.
RCM Analyzer
Perform RCM analysis to identify failure modes and determine optimum maintenance strategies. The RCM Analyzer uses the 7-Step SAE JA1011 RCM process. With the RCM Analyzer you can manage analysis work flow and approval processes and access technical and project management reports for insight into RCM analysis progress and realized benefits. This historical log allows you to evaluate preventive maintenance task changes over time and provides an audit trail to your PM program.
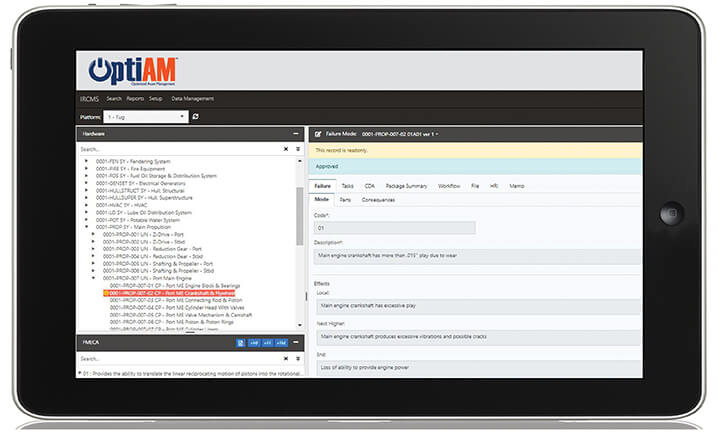
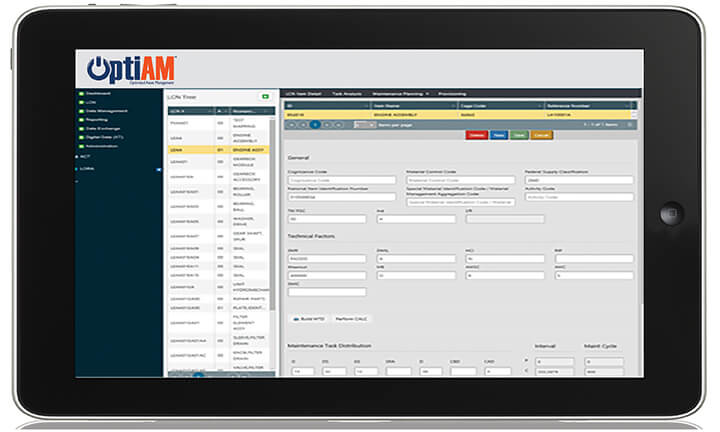
Supportability Analyzer
The Supportability Analyzer tool is a scalable, robust web-based application. Built on the Microsoft.Net and SQL Server technology stack it can easily be integrated with any compatible business intelligence tool for data mining and analytics. It supports both SaaS on AWS or in premise installation and flexible license models. Supports standard summary reports and saves time with find and search features. Training and customer support come standard, minimizing the adoption and learning curve times. It can be extended to meet the data exchange requirements for ASD/AIA S series of ILS specifications.
Task Developer
Develop the procedures and identify all of the resources needed to support your assets. Task Developer identifies resources needed to perform preventative and corrective maintenance tasks and groups these tasks into maintenance packages. The Task Developer can also generate maintenance manuals, standard operating procedures (SOP) and emergency operating procedures (EOP). Revisions can be tracked and releases controlled. Task Developer also creates automated checklists for use with the OptiChek™ and OptiAM® Mobile applications.
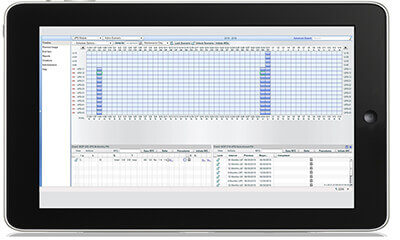
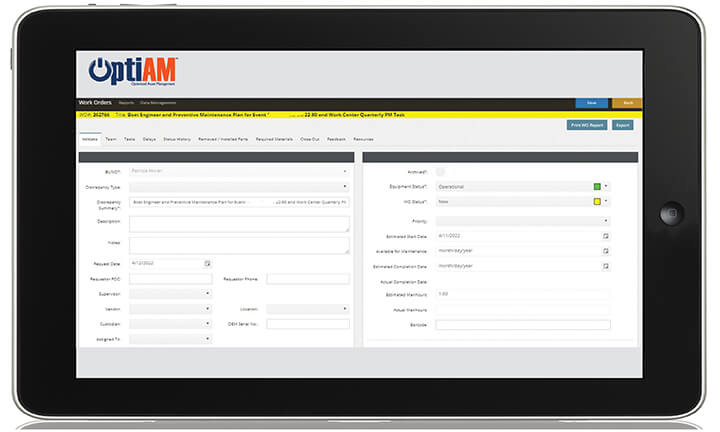
Work Order Manager
Optimize your maintenance schedule based on individual asset usage and environment to minimize down time or cost. The Maintenance Optimizer provides a full featured work order management system to schedule, manage, execute and document maintenance workload. It can also schedule actions such as contract or warranty renewals, planned upgrades and set alert triggers to generate automated work orders based on inputs from inspections, PdM or equipment monitoring systems. The Maintenance Optimizer provides near real-time equipment status to other modules in OptiAM®.
Supportability Optimizer
The one-of-a-kind Supportability Optimizer provides advanced modeling and simulation capabilities to evaluate your support infrastructure and identify optimum support solutions.
Supportability Optimizer will help answer questions such as:
- How many spares should I stock and where should I keep them?
- Should I establish repair capabilities and if so, how much and where should I locate it?
- What is an optimum maintenance outsourcing strategy and what is the potential ROI?
- What is the optimum replacement strategy for an asset?
The Supportability Optimizer will allow you to more accurately predict the support cost components of Total Ownership Cost than ever before. Because it is integrated within the OptiAM® suite, developing and modeling support scenarios is much faster and easier than using other stand-alone modeling or cost analysis tools.
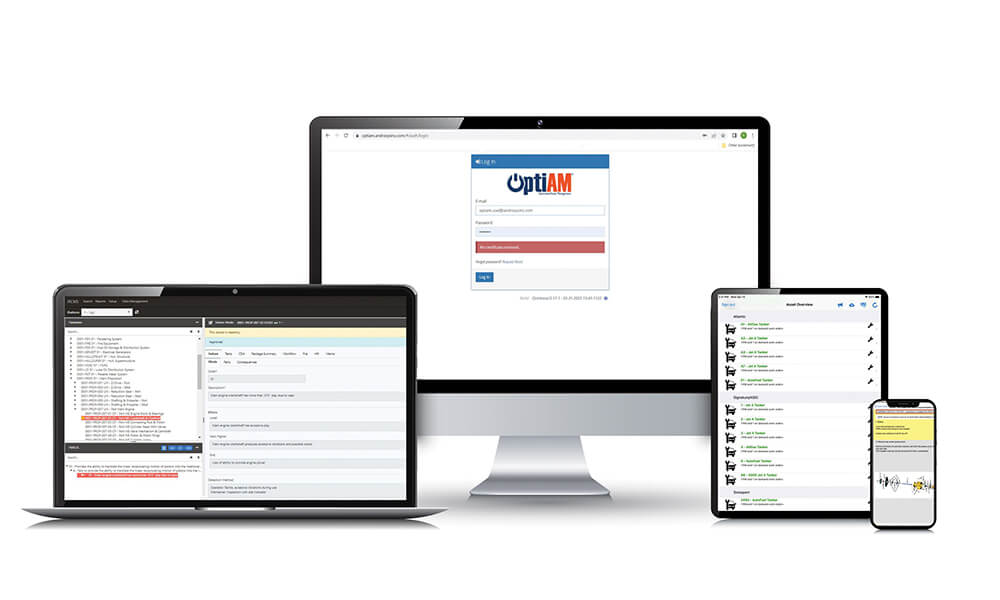
Book a Demo
Learn how OptiAM® Enterprise Asset Management software will benefit your business. We provide a customized tour and answer your questions.
OptiAM® Guide
Download our OptiAM® brochure for a more in-depth guide to our Enterprise Asset Management software.
What our OptiAM® clients are saying…
Corporate Headquarters
440 Viking Drive, Suite 230
Virginia Beach, VA 23452
Corporate Office
6255 Lake Gray Blvd., Suite 4
Jacksonville, FL 32244
USA Offices
Crystal City, VA
Havelock, NC
Oklahoma City, OK
Patuxent River, MD
San Diego, CA
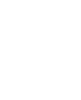
Get in Touch
904-637-2020
Follow Us
Email Us
"*" indicates required fields