About FMECA Training
Failure Mode, Effects, Criticality Analysis is a process similar to other Failure Modes and Effects Analyses (FMEA), but it is focused on identifying those failure modes that will possibly occur in-service and will likely need remediation, restoration and/or prevention during the life of the equipment.
In contrast to a design FMEA which is focused on the elimination of defects at piece-part levels, FMECA focuses on the systems, components, and levels of indenture that the users of the equipment will likely have to repair and perform maintenance on. The FMECA also adds a criticality analysis that aids in prioritizing failure modes for further analysis and decisions on where resources should be applied. An FMECA is typically less intensive than a traditional design FMEA. A proper FMECA is the foundation for all other supportability analyses.
Our FMECA training provides attendees with the knowledge to begin performing a Failure Mode, Effects, and Criticality Analysis. For Supportability or Logistics Engineers involved in performing supportability analysis, this course will provide an understanding of how the FMECA process supports the supportability analysis process and the importance of correctly identifying failure modes to ensure that supportability analysis is performed accurately and efficiently. This training is especially beneficial to those involved in Reliability-Centered Maintenance analysis projects or other efforts focused on improving maintenance processes or in-service reliability.
The Goal
FMECA aims to identify those failures that may occur in the life of a physical asset or fleet and require remediation. Learn the analysis methods used by leading OEMs, Program and Asset Managers, and Supportability experts to develop support programs that ensure reliability and optimum performance in your assets. These techniques can be applied formally or informally in any industry including military, industrial, or fleet environments.
Types of FMECA Training
This introductory course offering provides practical instruction and application in performing FMECA. The current course offering is intended for anyone performing Product Support Analysis (PSA) or FMECA in support of PSA.
For All Levels
FMECA • 2 days • Introduction to Failure Mode, Effects, Criticality Analysis
Benefits of FMECA Training
- Develop an understanding of PSA disciplines and how they can improve support programs
- Theory and practical experience needed to implement and perform FMECA
- Practical examples of the application of FMECA that will improve speed and quality of future analysis efforts
- An understanding of FMECA’s role and how to implement them throughout the asset lifecycle
- How to use them to identify opportunities that may warrant a more in-depth reliability analysis
Who is FMECA for?
FMECA training is beneficial to anyone performing Product Support Analysis (PSA) or FMECA in support of PSA specifically:
- Fleet/asset managers
- Maintenance planners/managers
- Reliability managers/engineers
- Field service representatives
- Logisticians
- Supportability professionals
History of FMECA
The FMECA (Failure Mode, Effects, Criticality Analysis) process was originally developed by the U.S military and document in the publication of MIL–P–1629. By the early 1960s, NASA and its contractors began incorporated variations of FMECA in their development of various spacecraft including Apollo, Viking, Voyager, Magellan, and Galileo, releasing a formal FMECA procedure in 1966.
At about the same time, Civil Aviation also began using FMECA. In 1967 the Society for Automotive Engineers (SAE) released its first publication to address FMECA for aviation SAE ARP926 . Today civil aviation continues to use both FMEA and related Fault Tree Analysis per SAE ARP4761.
In the 1970s, Ford Motor Company began using FMEA after experiencing problems related to the Ford Pinto. Its adoption by Ford led to widespread use across the automotive industry. By 1985, in Europe, the International Electrotechnical Commission published IEC 812 (now IEC 60812), addressing FMEA and FMECA for general use and The British Standards Institute published BS 5760–5 in 1991 for general purpose.
In 1980, MIL–STD–1629A replaced both MIL–STD–1629 and the 1977 aeronautical FMECA standard MIL–STD–2070. MIL–STD–1629A was canceled without replacement in 1998 but remains in use for military and space applications today and is widely referenced in many other industries.
Pricing
Training $799 USD per student.
For more information please contact us at: edu.pierian@androsysinc.com
Group Discounts Available.
FMECA Training Course Description
FMECA
Introduction to Failure Mode, Effects, Criticality Analysis
Introduction to the Failure Mode, Effects, and Criticality Analysis (FMECA) process as it is applied for use in a supportability analysis. The course provides practical instruction and practical application in performing a supportability FMECA and is based on MIL-STD-1629 as well as a future supportability FMECA being developed by the Society of Automotive Engineers (SAE). Intended for anyone performing Product Support Analysis (PSA) or FMECA in support of PSA.
FMECA - Failure Mode, Effects, Criticality Analysis Course Schedule
2025 Events Coming Soon - Fundamentals of Failure Mode, Effects, Criticality Analysis (FMECA) - $799.00
Training Information Request
We’re happy to answer you questions about our training courses. Get in contact with our team today.
"*" indicates required fields
Call or email for pricing, registration information, discounts for multiple attendees and government employees.
Corporate Headquarters
440 Viking Drive, Suite 230
Virginia Beach, VA 23452
Corporate Office
6255 Lake Gray Blvd., Suite 4
Jacksonville, FL 32244
USA Offices
Crystal City, VA
Havelock, NC
Oklahoma City, OK
Patuxent River, MD
San Diego, CA
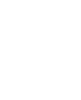
Get in Touch
904-637-2020
Follow Us
Email Us
"*" indicates required fields